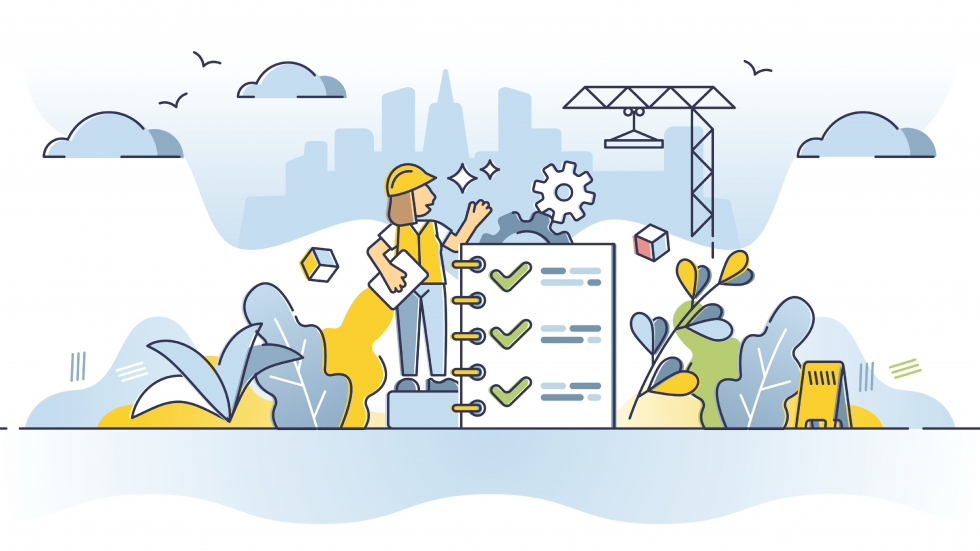
Dr. Letitia Heshmat is the founder and president of
Roseville-based Work Health Solutions. (Photo courtesy of Dr.
Letitia Heshmat)
Injuries incurring at your workplace may
seem inevitable, and to a certain degree this is true. But
analyzing the number of injuries that occur and the severity of
those injuries should also matter to a company that prioritizes
meeting deadlines and staying on track in a competitive
environment. So how should a company plan to minimize the
frequency and intensity of injuries on the job?
The answer may not be as hard as you think — prevention. Yes, we
have all heard the saying from Benjamin Franklin — “An ounce of
prevention is worth a pound of cure.” These are amazing words of
wisdom from someone in the 1700s that still hold true today,
especially in the workplace.
The staggering statistics
What Franklin noted is that it’s much smarter, and cheaper, to
prevent something from happening rather than having to fix it
once it has occurred. It’s probably safe to assume that Franklin
did not realize how much, in the future, American businesses
would be spending to help injured employees and could not have
even imagined what that amount equals in today’s economy. For
instance, The Liberty Mutual Workplace Safety Index 2020 reports
that serious, nonfatal workplace injuries are costing U.S.
businesses more than $1 billion dollars each week.
And, according to the National Institute for Occupational Safety
& Health, a recent economic analysis suggested that traumatic
occupational deaths and injuries cost the nation $192 billion
annually, taking into account both direct medical costs and
indirect costs.
Indirect costs, which many businesses don’t often take into
consideration, can also be devastating. According to OSHA, these
include: training replacement employees, accident investigation
and implementation of corrective measures, lost productivity,
repairs of damaged equipment and property, and costs associated
with lower employee morale and absenteeism. Add to that list the
cost of buying replacement equipment if damages cannot be
repaired. Other hidden costs are recruiting and providing
benefits for replacement workers, and the fact that the company
is now paying twice the benefit costs for one position.
Prevention programs are the key
With prevention measures in place, these unfortunate statistics
can be changed. Within these staggering numbers are three of the
top 10 injury causes — handling objects, working in awkward
positions and repetitive motions involving microtasks. These
injuries could all be lessened by implementing an injury
prevention program designed by analyzing work environments to
determine changes that can be made to avoid the most common
injuries likely to occur in your workplace, providing education
about proper ergonomics, and offering stretching and
strength-building exercises.
Instead of being reactive with your health care services after an
injury occurs, employers can potentially avoid the injury
altogether with injury prevention specialists who are certified
athletic trainers that use the sports medicine model of care
predicated on prevention and early intervention.
Investing in safety can equal big savings
As we head into a possible recession, it is important to
understand this concept as most employers’ first instinct will be
to cut costs on safety protocols. But rest assured, cutting back
on these initiatives can and will lead to higher costs. There can
also be a significant loss of employee confidence in your ability
to keep them safe, and once employees doubt if you care about
their well-being, it is a tough road trying to rebuild that
trust.
Companies that invest in injury prevention programs to bolster
workplace safety and health can expect to reduce fatalities,
injuries and illnesses; lower medical expenses and workers’
compensation costs; and make significant improvements in
productivity and financial performance. In fact, one study
estimates that for every dollar spent on safety protocols in the
workplace, injury prevention returns can range anywhere from
$2 to $6. Who wouldn’t gladly spend $1 now to ultimately save up
to $6? But unfortunately, when faced with a recession, it is hard
to fully comprehend the long-term benefits of prevention as many
employers will be tempted to simply cut safety measures to
experience an immediate reduction in expenses.
It takes real foresight to understand that, in the long run, the
cost of injury prevention is far less than the cost of an
injury. Here is another old saying that is relevant — “Penny
wise and pound foolish.” Neglecting to implement prevention
measures may save a few pennies now, but it can cost you plenty
of pounds later.
Dr. Letitia Heshmat is the founder and president of
Roseville-based Work Health Solutions, providers of
concierge-style occupational medicine for large-scale employers
nationwide. She has nearly two decades of health care industry
experience and previously served as director of the occupational
health clinic at Stanford University.
–
Stay up to date on business trends in the Capital
Region and beyond: Subscribe to the
Comstock’s newsletter today.